Hallo Leute,
ich hatte mich hier ja schonmal kurz zu Wort gemeldet nun aber etwas ausführlicher und mit der Hoffnung hier noch einige Tipps und oder Anregugngen zu bekommen.
Zur Person: Mein Name ist Alexander ich bin 21 Jahre alt und bin Azubi Elektroniker für Geräte und Systeme im 2. Lehrjahr.
Geschichte(Wems zu langweilig ist weiter runterscrollen):
Die Gundsatzidee war mal eine kleine Fräse zur Frontplattenhertstellung zu besitzen. Daraus wurde aber schnell der umfangreichere Wunsch damit auch mal richtiges Alu bearbeiten zu können. Als unerfahrener also ins Internet und irgendeine Fräse bestellt weil das Geld gerade da war. Damit kräftig auf die Schnauze gefallen und ca. 1500€ in den Sand gesetzt. Dann der Entschluss Selbstbau. Viel gelesen viel gelernt angefangen zu entwerfen (Bin fitt mit Inventor) und wieder verworfen. Irgendwann hatte ich mich dann auf ein Konzept Eingeschossen. Kaum hatte ich die ersten Teile bestellt tauchte Karls Thread hier auf und schmiss meine Vorstellungen wieder über den Haufen.
Trotzdem bin ich erstmal bei meinem Konzept geblieben, wird ja schon gut gehen. Also eine Menge Teile bearbeitet und zugerichtet. Nun habe ich vor ein paar Tagen angefangen das Puzzle zusammen zu setzen und werde mit jedem Teil immer unsicherer ob ich nicht doch wieder eine Menge Geld in den Sand gesetzt habe.
So nun ein paar Bilder:
Verwendetes Material:
Blau lackierte Teile sind aus Stahl mit überfrästen Auflageflächen für die Profile und die Wagen etc.
Aluminium als Adapterplatte für Z
Z-Achse ist eine Hiwin Kompaktachse aus Stahl
Führungen sind alle ARC20 von CPC/Romani mit langen Wagen V1 Vorspannung
Spindeln an XY sind 16/5 von Isel gelagert mit Fest und Loslager nach EMS
Profile sind auf Y (lange Achse) 60x40 Nut5 mit Sand 2/3 nicht überfräst
Profile sind auf X 40x40 Nut5 mit Sand 2/3 nicht überfräst
Bekannte Schwachstellen:
Stahl -> schwer (Dynamik)
Profile könnten stärker sein
Stützweiten zu gering
Zu Verfügung stehende Messmittel:
Stahllineal wie von Karl empfohlen 17um Ebenheitsfehler
Messuhr 1/100 + Stativ
Fühlmessheber 1/100 + Stativ
Haarwinkel
Anschlagwinkel groß
Fühlerlehre
Fragen die sich bei Aufbau ergeben haben:
Wie genau muss man Linearführungen zueinander einmessen? Reicht es wenn die Achse frei läuft oder würde man eine Verspannung unter Umständen gar nicht mitbekommen?
Unabhängig von den bekannten Schwachstellen meiner Konstruktion. Gibt es irgendetwas was man noch verbessern kann damit das Teil nachher einigermaßen vernünftig in Alu funktioniert? (Wir reden hier von 1/10 Toleranzen)
Wäre cool wenn ihr mal euren Senf dazugebt. Ich schau mal das ich noch ein paar Fotos hochlade... Das klappt aber gerade nicht so gut.
gruß Alex
ich hatte mich hier ja schonmal kurz zu Wort gemeldet nun aber etwas ausführlicher und mit der Hoffnung hier noch einige Tipps und oder Anregugngen zu bekommen.
Zur Person: Mein Name ist Alexander ich bin 21 Jahre alt und bin Azubi Elektroniker für Geräte und Systeme im 2. Lehrjahr.
Geschichte(Wems zu langweilig ist weiter runterscrollen):
Die Gundsatzidee war mal eine kleine Fräse zur Frontplattenhertstellung zu besitzen. Daraus wurde aber schnell der umfangreichere Wunsch damit auch mal richtiges Alu bearbeiten zu können. Als unerfahrener also ins Internet und irgendeine Fräse bestellt weil das Geld gerade da war. Damit kräftig auf die Schnauze gefallen und ca. 1500€ in den Sand gesetzt. Dann der Entschluss Selbstbau. Viel gelesen viel gelernt angefangen zu entwerfen (Bin fitt mit Inventor) und wieder verworfen. Irgendwann hatte ich mich dann auf ein Konzept Eingeschossen. Kaum hatte ich die ersten Teile bestellt tauchte Karls Thread hier auf und schmiss meine Vorstellungen wieder über den Haufen.
Trotzdem bin ich erstmal bei meinem Konzept geblieben, wird ja schon gut gehen. Also eine Menge Teile bearbeitet und zugerichtet. Nun habe ich vor ein paar Tagen angefangen das Puzzle zusammen zu setzen und werde mit jedem Teil immer unsicherer ob ich nicht doch wieder eine Menge Geld in den Sand gesetzt habe.
So nun ein paar Bilder:
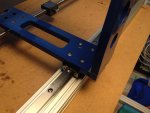
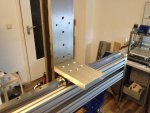
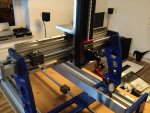
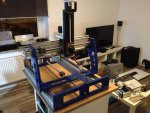
Verwendetes Material:
Blau lackierte Teile sind aus Stahl mit überfrästen Auflageflächen für die Profile und die Wagen etc.
Aluminium als Adapterplatte für Z
Z-Achse ist eine Hiwin Kompaktachse aus Stahl
Führungen sind alle ARC20 von CPC/Romani mit langen Wagen V1 Vorspannung
Spindeln an XY sind 16/5 von Isel gelagert mit Fest und Loslager nach EMS
Profile sind auf Y (lange Achse) 60x40 Nut5 mit Sand 2/3 nicht überfräst
Profile sind auf X 40x40 Nut5 mit Sand 2/3 nicht überfräst
Bekannte Schwachstellen:
Stahl -> schwer (Dynamik)
Profile könnten stärker sein
Stützweiten zu gering
Zu Verfügung stehende Messmittel:
Stahllineal wie von Karl empfohlen 17um Ebenheitsfehler
Messuhr 1/100 + Stativ
Fühlmessheber 1/100 + Stativ
Haarwinkel
Anschlagwinkel groß
Fühlerlehre
Fragen die sich bei Aufbau ergeben haben:
Wie genau muss man Linearführungen zueinander einmessen? Reicht es wenn die Achse frei läuft oder würde man eine Verspannung unter Umständen gar nicht mitbekommen?
Unabhängig von den bekannten Schwachstellen meiner Konstruktion. Gibt es irgendetwas was man noch verbessern kann damit das Teil nachher einigermaßen vernünftig in Alu funktioniert? (Wir reden hier von 1/10 Toleranzen)
Wäre cool wenn ihr mal euren Senf dazugebt. Ich schau mal das ich noch ein paar Fotos hochlade... Das klappt aber gerade nicht so gut.
gruß Alex
Zuletzt bearbeitet: